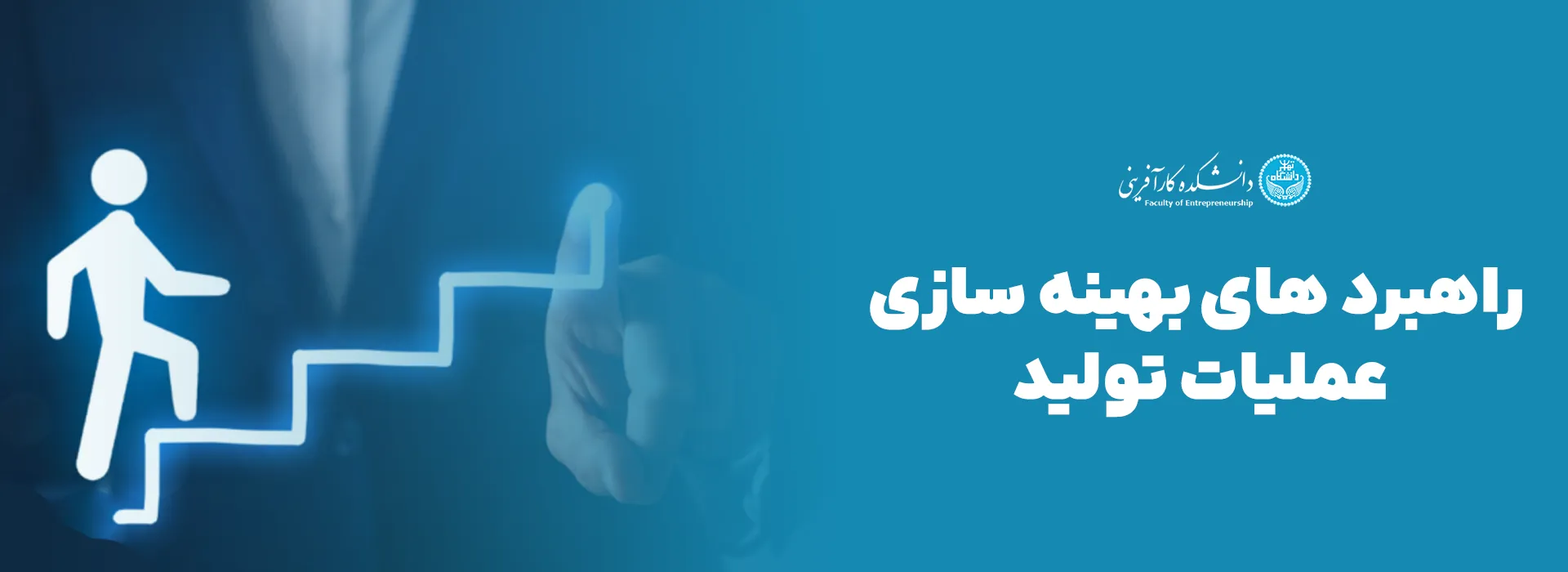
بهینهسازی عملیات تولید
بهینهسازی عملیات تولید یک فرآیند پیچیده و چندبعدی است که هدف اصلی آن افزایش کارایی و بهرهوری در واحدهای تولیدی است و در دوره های MBA به آن میپردازیم. این کار میتواند شامل بهبود در فرآیندها، کاهش هزینهها، استفاده بهینه از منابع و افزایش کیفیت محصول نهایی باشد. برای بهینهسازی عملیات تولید، باید به چند راهبرد کلیدی توجه کرد که در ادامه توضیح داده میشوند.
بهینهسازی عملیات تولید شامل افزایش کارایی و بهرهوری از طریق بهبود فرآیندها، کاهش هزینهها و استفاده بهینه از منابع است. این راهبردها شامل تحلیل جریان کاری برای شناسایی گلوگاهها، بهرهگیری از فناوریهای نوین مثل IoT و هوش مصنوعی، و بهکارگیری مدیریت کیفیت جامع میشود. بهبود هماهنگی بین بخشهای مختلف و تقویت ارتباطات، آموزش کارکنان برای سازگاری با تغییرات، و بهینهسازی مصرف انرژی نیز از جنبههای کلیدی بهینهسازی تولید هستند. این فرآیندها با فرهنگ بهبود مستمر و استفاده از دادهها برای تصمیمگیری میتوانند به افزایش کیفیت و کاهش هزینهها کمک کنند و در نهایت موجب پایداری و موفقیت واحد تولیدی شوند.
تجزیه و تحلیل جریان کاری
یکی از اولین گامها برای بهینهسازی عملیات تولید، تجزیه و تحلیل جریان کاری است. این فرآیند شامل شناسایی گلوگاهها و نقاط ضعف در چرخه تولید است. در بسیاری از موارد، این گلوگاهها میتوانند فرآیندهای کند یا ناکارآمدی باشند که باعث تأخیر در تولید میشوند. با استفاده از ابزارهایی مانند نمودار جریان یا تحلیل زمان و حرکت، میتوان مشکلات اصلی را شناسایی کرده و راهکارهایی برای حل آنها پیشنهاد داد. از جمله این راهکارها میتوان به تغییر ترتیب مراحل تولید یا استفاده از تکنولوژیهای جدید برای خودکارسازی فرآیندها اشاره کرد.
استفاده از فناوریهای جدید
تکنولوژی نقش بسیار مهمی در بهینهسازی عملیات تولید ایفا میکند. استفاده از سیستمهای خودکار، مانند رباتها و تجهیزات هوشمند، میتواند به افزایش سرعت تولید و کاهش هزینهها کمک کند. به علاوه، فناوریهای نوین مانند اینترنت اشیاء (IoT)، دادههای بزرگ (Big Data)، و هوش مصنوعی (AI) میتوانند در جمعآوری و تحلیل دادهها، پیشبینی مشکلات پیش از وقوع و بهبود تصمیمگیریها مؤثر باشند.
برای مثال، با استفاده از IoT، ماشینآلات تولیدی میتوانند دادههایی مانند دما، فشار و زمان کارکرد را به طور مستمر ارسال کنند. این دادهها به کمک الگوریتمهای یادگیری ماشینی تحلیل شده و میتوانند الگوهای خرابی را شناسایی کنند. این کار به کاهش زمان تعطیلی ناخواسته ماشینآلات کمک میکند و باعث افزایش بهرهوری کلی سیستم میشود.
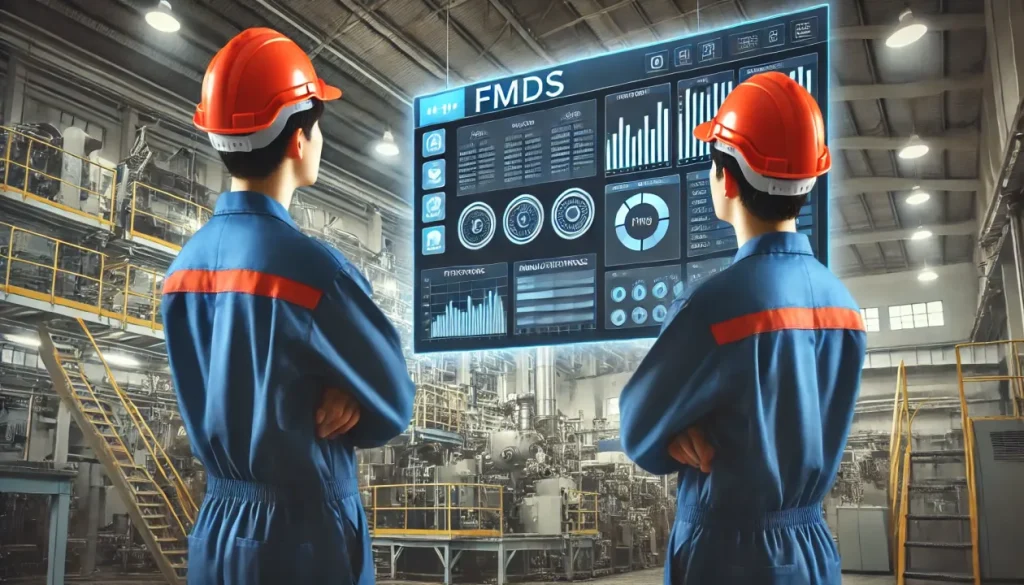
مدیریت کیفیت جامع (TQM)
مدیریت کیفیت جامع یکی از راهبردهای مهم در بهینهسازی عملیات تولید است. این رویکرد بر بهبود مستمر فرآیندها و توجه به کیفیت در تمام جنبههای تولید تأکید دارد. در این رویکرد، همه کارکنان، از مدیران تا کارگران خط تولید، باید در فرآیند بهبود کیفیت مشارکت داشته باشند.
استفاده از ابزارهای کنترل کیفیت مانند Six Sigma و کنترل آماری فرآیند (SPC) میتواند در کاهش ضایعات و بهبود کیفیت نهایی محصول نقش کلیدی داشته باشد. به علاوه، برقراری یک فرهنگ سازمانی که در آن کیفیت به عنوان یک ارزش محوری تلقی شود، میتواند به بهبود مداوم تولید و رضایت مشتریان کمک کند.
بهبود ارتباطات و هماهنگی بین بخشها
در بسیاری از واحدهای تولیدی، ناکارآمدیها از عدم هماهنگی مناسب بین بخشهای مختلف مانند طراحی، تولید و تأمین منابع ناشی میشود. بهبود ارتباطات و هماهنگی بین این بخشها میتواند نقش بسزایی در بهینهسازی عملیات داشته باشد. برای مثال، تیمهای طراحی و تولید باید به طور منظم با یکدیگر ارتباط داشته باشند تا مطمئن شوند که محصولی که طراحی شده است، به طور کارآمد و با کمترین هزینه تولید شود.
همچنین، بهبود مدیریت زنجیره تأمین نیز میتواند تأثیر بسزایی در بهینهسازی عملیات تولید داشته باشد. استفاده از سیستمهای پیشرفته برای مدیریت زنجیره تأمین، مانند ERP (برنامهریزی منابع سازمانی)، میتواند در کاهش زمان تأخیر در تأمین مواد اولیه و جلوگیری از مشکلات موجودی کالا مؤثر باشد.
آموزش و توانمندسازی کارکنان
یکی از کلیدهای موفقیت در بهینهسازی تولید، سرمایهگذاری در آموزش و توانمندسازی کارکنان است. کارگران و مدیران واحدهای تولیدی باید آموزشهای لازم برای استفاده از تکنولوژیهای جدید، بهبود فرآیندهای تولید و حل مشکلات احتمالی را دریافت کنند. آموزشهای منظم و بهروز میتواند به کارکنان کمک کند تا بهرهوری خود را افزایش دهند و با تغییرات محیط کاری بهتر سازگار شوند.
همچنین، تشویق به نوآوری و مشارکت کارکنان در فرآیندهای بهبود میتواند منجر به شناسایی راهکارهای خلاقانه برای حل مشکلات تولید شود. در بسیاری از موارد، کارکنانی که به طور مستقیم در فرآیندهای تولید درگیر هستند، بهترین بینشها را درباره مشکلات و فرصتهای بهبود دارند.
بهینهسازی مصرف انرژی و منابع
در بسیاری از واحدهای تولیدی، مصرف انرژی یکی از بزرگترین هزینههاست. بهینهسازی مصرف انرژی و منابع میتواند به کاهش هزینهها و همچنین بهبود پایداری محیطی منجر شود. استفاده از تجهیزات کممصرف، بهینهسازی فرآیندهای تولیدی و استفاده از انرژیهای تجدیدپذیر میتواند در این زمینه مؤثر باشد.
برای مثال، استفاده از سیستمهای مدیریت انرژی میتواند به کنترل و کاهش مصرف انرژی در واحدهای تولیدی کمک کند. این سیستمها میتوانند به شناسایی نقاط پرمصرف در خط تولید کمک کرده و راهکارهایی برای کاهش مصرف انرژی پیشنهاد دهند.
توسعه فرهنگ بهبود مستمر (Kaizen)
Kaizen، که در زبان ژاپنی به معنای “بهبود مستمر” است، یکی از راهبردهای موفق در بهینهسازی عملیات تولید است. این رویکرد بر این اصل استوار است که حتی کوچکترین بهبودها نیز میتوانند در طول زمان تأثیر بزرگی داشته باشند. فرهنگ Kaizen تشویق میکند که کارکنان در همه سطوح به بهبود فرآیندها، کاهش ضایعات و افزایش بهرهوری توجه کنند.
Kaizen معمولاً با جلسات روزانه کوتاه و منظم همراه است که در آن کارکنان مشکلات خود را مطرح کرده و با کمک مدیران به دنبال راهحلهای مناسب میگردند. این روش نه تنها باعث بهبود فرآیندهای تولید میشود، بلکه به تقویت همکاری و افزایش رضایت کارکنان نیز کمک میکند.
استفاده از دادهها برای تصمیمگیری
تحلیل دادهها و استفاده از اطلاعات واقعی در فرآیند تصمیمگیری میتواند به بهینهسازی عملیات تولید کمک زیادی کند. جمعآوری و تحلیل دادهها از مراحل مختلف تولید به مدیران این امکان را میدهد که مشکلات را پیشبینی کرده و تصمیمات مبتنی بر شواهد بگیرند.
در بسیاری از واحدهای تولیدی پیشرفته، از سیستمهای ERP و نرمافزارهای مدیریت تولید برای جمعآوری و تحلیل دادهها استفاده میشود. این سیستمها به مدیران کمک میکنند تا عملکرد ماشینآلات، کیفیت محصولات، و مصرف منابع را در زمان واقعی پیگیری کرده و اقدامات به موقع برای بهبود عملکرد انجام دهند.
بهینهسازی عملیات تولید یک فرآیند چندوجهی است که نیازمند توجه به تکنولوژی، فرآیندها، و نیروی انسانی است. از طریق تجزیه و تحلیل جریان کاری، استفاده از فناوریهای نوین، مدیریت کیفیت جامع، بهبود ارتباطات، آموزش کارکنان، بهینهسازی مصرف انرژی و استفاده از دادهها میتوان به بهبود مستمر در تولید دست یافت. در نهایت، توسعه فرهنگ بهبود مستمر و تشویق به نوآوری در تمام سطوح سازمانی از عوامل کلیدی در موفقیت بهینهسازی عملیات تولید محسوب میشوند.